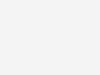
The Basics
Thermoforming Molds 101
There are two main types of thermoforming processes. Sheet thickness less than 1.5 mm (0.060 inches) is usually delivered to the thermoforming machine from rolls or a sheet extruder. Thin-gauge roll-fed or inline extruded thermoforming applications are dominated by rigid or semi-rigid disposable packaging. Sheet thicknesses greater than 3 mm (0.120 inches) are usually delivered to the forming machine by hand or an auto-feed method already cut to final dimensions. Heavy, or thick-gauge, cut sheet thermoforming applications are primarily used as permanent structural components.
Heavy-gauge forming utilizes the same basic process as continuous thin-gauge sheet forming, typically draping a heated plastic sheet over a mold. Many heavy-gauge forming applications use vacuum only in forming, although some use two halves of mating form tooling and include air pressure to help form. Aircraft windscreens and machine gun turret windows spurred the development of heavy-gauge forming technology during WWII. Heavy gauge parts are used as cosmetic surfaces on permanent structures such as automobiles, refrigerators, spas, and shower enclosures, and electrical and electronic equipment. Unlike most thin-gauge thermoformed parts, heavy-gauge parts are often hand-worked after forming for trimming to final shape or for additional drilling, cutting, or finishing, depending on the product. Heavy-gauge products typically are of a "permanent" end-use nature, while thin-gauge parts are more often designed to be disposable or recyclable and are primarily used to package or contain a food item or product.
An integral part of the thermoforming process is the tooling or mold which is specific to each part to be produced. Thick or heavy gauge thermoforming also requires tooling specific to each part, but because the part size can be very large, the molds are generally ceramic composite thermoformng molds. Extreme voluimes may require cast aluminum.. Typically thick gauge parts must be trimmed on CNC routers or hand trimmed using saws or hand routers. Even the most sophisticated thermoforming machine is limited to the quality of the tooling. Some large thermoforming manufacturers choose to have design and tool-making facilities in-house but most rely on outside tool-making shops like Prestige Tooling, LLC to build the tooling or mold.