Vacuum forming VS Injection Molding 101
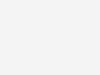
Two processes: Vacuum Forming VS Injection Molding
Vacuum forming and injection molding are two of the most popular methods used to process plastics. Prestige Tooling specializes in Ceramic Vacuum Forming molds, but is vacuum forming the right process for you? Depending on your budget and the quantity of parts you’ll need, it just might be.
What is Vacuum Forming?
Vacuum forming (also known as “thermoforming”) is a manufacturing process in which plastic sheet goods are preheated in automated vacuum forming equipment until soft and pliable. Next, the preheated sheet makes contact with a mold or form and a vacuum source is turned on, which “sucks” the sheet to the mold. Once cooled, the sheet takes the shape of the mold. It is then trimmed with either a 5 axis CNC router or simply hand cut. If additional detail is required, positive air pressure is used to assist the forming process, a technique commonly known as “pressure forming.”
Vacuum forming molds can be either “male” or “female,” depending on the geometry of the parts and where the weakest areas require more material thickness. Molds can be textured to impart different finishes using a female mold and positive air pressure.
What is Injection Molding?
Injection molding is a far more complex manufacturing technique than vacuum forming and requires a great deal of engineering. The process of injection molding begins with either pellets or granules of polymer which are placed in a hopper and then dropped into a barrel. A screw pushes the material into a heater where it is melted. Next, the liquid polymer is injected into a steel or aluminum split-die through a “gate” being held in a “press” under extreme pressure. After cooling, the die opens and pins eject the finished parts.
A great amount of engineering time and cost is required to fabricate the parts and dies used in injection molding, making vacuum forming the preferred process for many applications where time-to-market and low cost is critical. Still, each method has its own distinct merits and also unique drawbacks.
Advantages of Vacuum Forming
- Ability to create large parts
- Relatively fast prototyping and production time frames, sometimes as quickly as 2 weeks
- Lower start up costs — patterns and molds can be made inexpensively from our Ceramic vacuum forming process
- Good price point on small and medium runs
Disadvantages of Vacuum Forming
- Intricacy of parts is limited — additional details can be added with pressure forming
- Some clear parts will exhibit “mark-off” (i.e., defects or dirt from mold will transfer to parts)
- Consistent wall thickness is not possible — very deep parts can be problematic
- Higher per-piece costs make vacuum forming non-competitive with other automated processes where quantities are larger
- Only one material can be formed at a time
- Finishing costs can be costly and labor intensive
Advantages of Injection Molding
- Allows for high production output rates
- Can use inserts within the mold and fillers for added strength
- Close tolerances on small intricate parts are possible
- More than one material can be used at the same time when utilizing co-injection molding
- Typically requires very little post-production work — ejected parts usually have a very finished look
- Lower cost-per-part compared to vacuum forming
Disadvantages of Injection Molding
- Extremely high start-up costs
- Requires a great deal of engineering time
- Long time frames necessary to fabricate tooling, making time-to-market a major drawback
In summary, both processes have their advantages and disadvantages. In determining which method is best for your particular product, consider these issues: production quantity, design and engineering requirements, time frame, start-up costs and overall budgetary concerns. For additional information on ceramic vacuum forming molds, give Prestige Tooling a call.