Ceramic Composite Thermoforming Molds
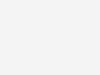
Molds for Pressure Forming and Vacuum Forming
Prestige Tooling has been providing molds for vacuum and pressure forming nationwide for over 20 years. What are the differences between the two processes?
Thermoforming is a method of processing plastic resin into finished parts from sheet or film. The plastic sheet is heated to its particular thermoforming temperature and immediately shaped into the desired configuration. At processing temperatures, the sheet is very pliable, enabling it to be formed rapidly with great detail and minimum force. Pressure is maintained until the part has cooled
Prestige Tooling provides molds for two particular types of thermoforming processes:
1. Vacuum Forming molds: With vacuum forming, a positive or negative mold of the desired part is created and mounted into vacuum forming machine. A sheet of plastic (a blank) is clamped into the clamp frame of the vacuum forming machine to ensure the sheet is held firmly in place during the vacuum forming process. The plastic blank is retracted into the heating oven where it heats to the required forming temperature. Once heated, the plastic blank is moved out of the oven and over the positive or negative mold. The plastic sheet is then draped over the mold and a vacuum is applied to quickly remove the air between them. Removing the air between the mold and the plastic blank allows atmospheric pressure to move (form) the pliable plastic to the mold. Cooling is applied once the plastic is formed to the shape. When the part has cooled, it can be removed form the mold. There are several techniques applied in the vacuum forming process. Each technique depends on the design of the part being formed. We discuss vacuum forming techniques in a separate blog post.
2. Pressure Forming: To thermoform plastic parts that require more design detail such as sharp edges, close dimensional tolerances, and detailed surface shapes, pressure forming would be used over vacuum forming. Pressure forming applies high pressure to the plastic blank along with the vacuum to form the desired part. Common pressures are 35 to 60 PSI, however, higher pressures may be required for large parts of higher hot strength materials. The heated plastic blank is draped into a negative mold and a pressure plate is clamped on top of the negative mold. Vacuum is applied to remove the ambient air between the mold and the plastic sheet, and compressed air is used to pressurize the empty space in the mold cavity. The added pressure literally pushes (forces) the pliable plastic into the negative mold shape forcing sharp edges, undercuts, and other high tolerance design shapes. The vacuum and pressure are applied until the part cools and can be removed from the mold.
As with vacuum forming, there are several pressure forming techniques used depending on the design of the part being formed.
Feel free to contact Prestige Tooling with any questions or feedback.
For more basic information on thermoforming molds and the various processes, see the Wikipedia links below: